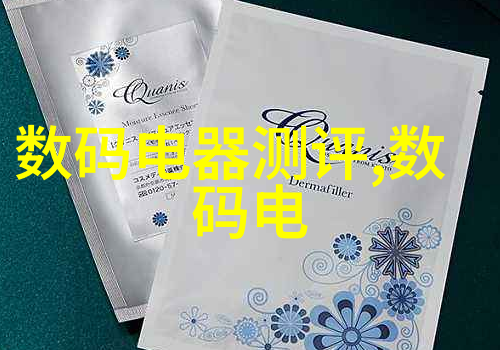
自动化控制系统在反应罐中的应用
引言
反应罐作为化学实验和工业生产中不可或缺的设备,其作用主要是用于储存、混合和反应各种化学品。随着科技的发展,传统的操作方式越来越难以满足现代化生产对效率和安全性的要求,因此引入了自动化控制系统,这种技术不仅提高了工作效率,还大幅度降低了人为错误带来的风险。
反应罐的基本作用与应用
反应罐能够承受高压、高温等恶劣条件,对于需要长时间搅拌或保温的化学反应尤其重要。它们通常由耐腐蚀材料制成,如不锈钢、陶瓷等,并配备精密搅拌装置,以确保反应物料充分混合。这些容器广泛应用于药物研发、有机合成、新能源材料制造等领域。
自动化控制系统概述
自动化控制系统通过集成传感器、执行器和计算机程序实现对反馈循环过程的监控与调节。在反应罐中,它可以实时监测温度、压力、流量等参数,并根据预设规则进行调整,以保持最佳运行状态。
控制策略及其优点
自动化控制策略包括PID(比例-积分-微分)控制、三级或者多级调节等。这类策略能够快速响应变化,减少过载情况,提高整个工艺流程的稳定性。同时,由于操作人员参与较少,自动化系统降低了操作误差并且提升了工作安全性。
实际案例分析
例如,在某生物医药公司,一款新型疫苗研发项目中使用到了大量复杂化学步骤,其中一个关键步骤就是在特定的条件下进行蛋白质纯化。这项任务非常依赖于温度和搅拌速度的一致性,如果手动操作可能会导致产品质量波动。而通过安装自动化控制系统,可以保证每次都是在最优条件下完成,从而提高产品纯度和一致性。
安全考虑与事故处理方案
虽然自动化显著提升了安全性,但仍需考虑潜在故障,如传感器失灵或软件bug引起的问题。此外,当出现异常时,需要迅速切断电源并采取紧急措施,比如隔离泄漏区域防止扩散。此外,对于已发生事故,有效的事故报告能帮助改进设计以避免未来再次发生类似事件。
未来趋势与展望
随着AI、大数据以及智能制造技术的融合,将推动更先进、高效且可持续的人工智能驱动反馈循环管理。这将进一步增强反馈数据分析能力,使得设备能够更加自主地做出决策,为未来的高端研究提供支持,同时也促进环境友好型工业革命前行。
结论
总结来说,自动化控制系统极大地拓宽了一些原本只能用人工完成任务的手段,让我们可以更深入地探索科学知识边界,同时对于工业生产模式亦构成了重大变革,为绿色经济发展提供新的可能性。